Demystifying Industrial Weighing Scales Legal Compliance: A Complete Guide
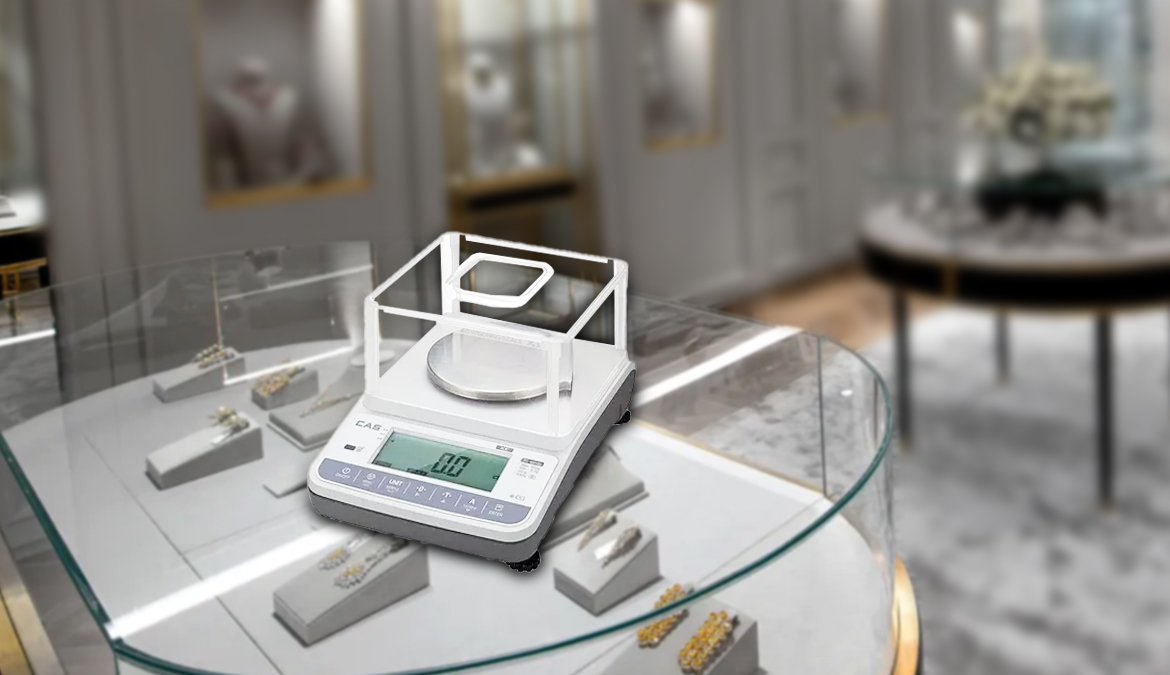
Do you find yourself tangled in the complexities of ensuring your industrial weighing scales comply with legal standards? Imagine the peace of mind that comes with demystifying these regulations and having a clear path to compliance.
In our complete guide on industrial weighing scales legal compliance, we address your pain points head-on and provide expert insights to navigate this crucial aspect of your business operations. Let’s dive into the key topics we’ll cover:
Understanding the legal framework: We break down the regulatory landscape governing industrial weighing scales to simplify complexities.
Compliance checklist: Gain access to a practical checklist to ensure your weighing scales meet all necessary legal requirements.
Maintenance best practices: Discover expert tips on how to maintain and calibrate your scales to uphold compliance standards.
Case studies and real-life examples: Learn from real-world scenarios to understand the implications of non-compliance.
With our comprehensive guide, you’ll emerge equipped to navigate the legal intricacies of industrial weighing scales with confidence. Get ready to elevate your compliance game and streamline your operations effectively.
Short Summary
- Understand the regulatory landscape governing industrial weighing scales for simplified compliance.
- Utilize a practical checklist to ensure legal requirements are met for your weighing scales.
- Implement expert maintenance tips for scale calibration to uphold compliance standards.
- Learn from real-life examples to grasp the consequences of non-compliance in industrial weighing scales.
Table of Contents
Toggle1. Understanding Legal Requirements for Industrial Weighing Scales
Industrial weighing scales play a crucial role in various sectors, ensuring accurate measurements for commercial applications. However, to maintain compliance with legal metrology regulations, businesses must adhere to stringent standards and practices. Let’s delve into the key aspects of understanding the legal requirements for industrial weighing scales:
Importance of Legal Metrology
Legal metrology is the scientific study of measurement and its application in ensuring fair trade and consumer protection. It establishes the legal requirements for measuring instruments used in trade, such as weighing scales. Compliance with legal metrology standards is vital to maintain transparency and trust in commercial transactions.
Legal Framework and Certification
Legal Metrology Act: Businesses must comply with the Legal Metrology Act, which governs the use of measuring devices and pre-packaged goods.
Legal Metrology Rules: These rules provide specific guidelines on the operation and verification of weighing scales.
Legal Metrology Certificate: Obtaining a legal metrology certificate signifies that the weighing scale meets the prescribed standards and has been verified by an approved body.
Verification and Calibration
Verification Scale Division: Ensuring that the scale division meets the required standards for accurate measurements.
Repair Weights: Regular calibration and adjustment of scales using certified weights to maintain precision.
Compliance Procedures
Inspection by Measures Inspector: Authorized inspectors conduct routine checks to verify the accuracy and calibration of weighing scales.
Operation Guidelines: Following a set of international guidelines for the proper operation of weighing equipment.
Ensuring Accuracy and Compliance
National Institute of Standards: Partnering with accredited institutions for calibration and verification of scales.
Pre-pack Lines: Incorporating legal-for-trade scales in complete pre-pack lines to meet legal requirements.
Useful Resources
For further information on legal metrology applications and regulations, businesses can refer to published guidelines, related legislation, and useful links’ sections provided by the legal metrology department.
2. Importance of Legal Compliance in Industrial Weighing Scales
In the realm of industrial weighing scales, ensuring legal compliance is paramount for businesses that rely on accurate measurements for commercial transactions and regulatory adherence. Let’s delve into why legal compliance with regards to industrial weighing scales is not just a best practice but an essential requirement for businesses that utilize these precision instruments.
Why Legal Compliance Matters
- Accuracy and Fair Trade: Legal compliance guarantees that the readings displayed by industrial weighing scales are accurate and trustworthy. This ensures fair trade practices and prevents any discrepancies in measurements during commercial transactions.
- Regulatory Obligations: Adhering to legal metrology ensures that businesses comply with the regulations set forth by authorities to maintain uniform standards and uphold consumer protection laws related to measuring devices.
- Avoiding Penalties: Non-compliance with legal metrology regulations can result in hefty fines, legal sanctions, and damage to reputation. By following the prescribed standards, businesses can avoid the negative consequences of using non-compliant weighing scales.
Best Practices for Legal Compliance
- Regular Calibration: Industrial weighing scales should undergo regular calibration by an approved body to ensure accurate measurements and compliance with legal requirements.
- Documentation and Certification: Keeping proper records of calibration, verification, and maintenance activities, along with possessing the necessary legal metrology certificates, is crucial for demonstrating compliance.
- Training and Awareness: Educating staff on the correct operation of weighing scales, legal requirements, and the importance of compliance can help prevent unintentional violations and ensure smooth regulatory inspections.
3. Key Components of Legal Compliance for Industrial Weighing Scales
When it comes to ensuring legal compliance for industrial weighing scales, there are several key components that businesses need to consider. By adhering to these crucial aspects, companies can avoid potential legal pitfalls and maintain the integrity of their measurement processes. Let’s delve into the essential elements that constitute legal compliance for industrial weighing scales:
- Understanding Legal Metrology Requirements:
To ensure compliance with legal standards, businesses must have a solid grasp of legal metrology requirements. This includes understanding the legal metrology act, rules, and regulations that govern the use of weighing scales in commercial applications. By staying informed about legal metrology guidelines, businesses can ensure that their weighing scales meet the necessary legal standards.
- Calibration and Certification:
One of the fundamental aspects of legal compliance for industrial weighing scales is proper calibration and certification. It is essential to have weighing scales calibrated by an appropriate approved body to ensure accurate measurements. Additionally, obtaining a legal metrology certificate is crucial to demonstrate compliance with legal requirements and standards.
- Regular Verification and Maintenance:
To maintain legal compliance, businesses should conduct regular verification and maintenance of their industrial weighing scales. This involves checking the accuracy of the scales, verifying scale divisions, and ensuring that the equipment operates correctly. Regular maintenance and calibration help prevent the use of incorrect equipment and ensure that the scales meet legal-for-trade requirements.
- Compliance with International Guidelines:
Businesses that operate on a global scale must ensure that their industrial weighing scales comply with international guidelines set by organizations such as the International Organization of Legal Metrology (OIML). Adhering to a stringent set of international guidelines helps businesses align their weighing scale practices with global standards and facilitate trade across borders.
- Training and Education:
Ensuring legal compliance for industrial weighing scales also involves providing appropriate training and education to staff members responsible for operating the equipment. Training employees on the correct operation of the scales, understanding legal metrology applications, and following prescribed standards is essential for maintaining compliance.
- Documentation and Record-Keeping:
Proper documentation and record-keeping play a vital role in demonstrating legal compliance for industrial weighing scales. Maintaining records of calibration, verification, and repairs, as well as keeping track of related legislation and published guidelines, helps businesses uphold legal standards and respond to audits effectively.
4. Ensuring Accuracy and Precision in Industrial Weighing Scales
When it comes to industrial weighing scales, ensuring accuracy and precision is paramount to meet legal compliance standards and maintain operational efficiency. Here are key strategies to guarantee the reliability and accuracy of your weighing equipment:
- Calibration Process:
Regular calibration by a certified technician is essential to verify the accuracy of the weighing scale. Follow the manufacturer’s guidelines and recommended frequency for calibration to ensure precise measurements. Document all calibration activities, including dates, results, and any adjustments made to the scale.
- Verification Procedures:
Implement verification procedures in accordance with legal metrology requirements to validate the accuracy of the weighing scale. Conduct routine checks using certified test weights to confirm the scale’s performance. Keep detailed records of verification activities for compliance audits and traceability.
- Maintenance Practices:
Establish a proactive maintenance schedule to prevent malfunctions and maintain the accuracy of the weighing scale. Regularly inspect components such as load cells, displays, and connections for signs of wear or damage. Address any issues promptly and enlist the services of qualified technicians for repairs and servicing.
- Training and Education:
Provide comprehensive training to operators on the correct usage and handling of the weighing scale. Educate staff on best practices for calibration, maintenance, and troubleshooting to optimize scale performance. Foster a culture of accuracy and precision among employees to uphold quality standards.
- Quality Control Measures:
Implement quality control measures to monitor the performance of the weighing scale over time. Conduct periodic audits and random checks to assess the scale’s accuracy and identify any deviations. Implement corrective actions when discrepancies are detected to maintain compliance with legal standards.
In the realm of industrial weighing scales, accuracy and precision are non-negotiable aspects that directly impact legal compliance and operational efficiency. By following these best practices and incorporating them into your weighing scale management processes, you can ensure reliable and compliant weighing operations within your industrial setting.
5. Compliance Documentation for Industrial Weighing Scales
Ensuring legal compliance in industrial weighing scales is imperative for businesses to operate within the boundaries set by regulatory bodies. Compliance documentation serves as the foundation for upholding standards and meeting legal requirements. Here’s a detailed look into the essential aspects of compliance documentation for industrial weighing scales:
Legal Metrology Guidelines:
Understanding legal metrology guidelines is crucial for compliance. These guidelines outline the specific requirements that industrial weighing scales must adhere to in terms of accuracy, calibration, and usage.
Certification Process:
Obtaining a legal metrology certificate is a key step in compliance. This certification validates that the weighing scale meets the necessary standards and has been inspected by an approved body.
Record Keeping:
Maintaining detailed records of calibration, inspections, and repairs is essential for demonstrating compliance. Proper documentation provides a trail of accountability and ensures transparency in operations.
Compliance Audits:
Regular compliance audits by measures inspectors help verify that industrial weighing scales are operating within the legal framework. These audits assess the accuracy of measurements and adherence to legal requirements.
Use of Approved Bodies:
Utilizing appropriate approved bodies for calibration and verification ensures that industrial weighing scales meet legal-for-trade standards. Working with reputable bodies enhances credibility and trust in compliance processes.
Stringent Testing Procedures:
Adhering to a stringent set of test procedures is critical for validating the accuracy and reliability of industrial weighing scales. These tests help identify any discrepancies and ensure consistent performance.
Comprehensive Documentation:
Maintaining comprehensive documentation that includes verification reports, calibration certificates, and compliance records is vital for demonstrating adherence to legal requirements. Thorough documentation facilitates smooth operations and regulatory checks.
6. Common Legal Pitfalls in Industrial Weighing Scales Compliance
When it comes to ensuring legal compliance with industrial weighing scales, businesses must navigate through potential pitfalls to avoid costly mistakes. Being aware of common legal pitfalls can help companies uphold standards set by legal metrology authorities and maintain credibility in commercial applications.
- Lack of Proper Calibration and Verification
Maintaining accurate measurements is crucial for legal metrology compliance. Failing to calibrate and verify weighing scales regularly can lead to inaccuracies in measurements, raising concerns about the reliability and integrity of the measuring instrument.
- Non-Compliance with Legal Requirements
Ignorance of legal metrology regulations can result in non-compliance with prescribed standards. Businesses must familiarize themselves with the legal metrology act and rules applicable to their operations to ensure adherence to the stringent set of tests and certifications required.
- Use of Non-Approved Weighing Devices
Using weighing devices that have not been approved by the appropriate regulatory body can pose legal risks. It is essential to purchase weighing scales from legal metrology-certified suppliers to guarantee the accuracy and reliability of the measuring equipment.
- Incorrect Labeling and Documentation
Failure to provide accurate labeling and documentation for weighing scales can lead to legal implications. Businesses must ensure that all measuring devices are properly labeled with the required information, including verification scale divisions and legal metrology certificates.
- Inadequate Maintenance and Repair
Neglecting the maintenance and repair of weighing scales can compromise their accuracy and functionality. Regular inspections, repairs, and calibrations by qualified professionals are essential to ensure the proper operation of the equipment and compliance with legal metrology requirements.
- Lack of Training and Awareness
Insufficient training and awareness among staff members regarding legal metrology applications can result in operational errors. It is crucial for businesses to educate their employees on the correct use of weighing scales, adherence to legal standards, and the importance of compliance to prevent legal pitfalls.
7. Training and Education on Legal Compliance for Industrial Weighing Scales
As one delves into the complexities of legal compliance for industrial weighing scales, training and education play a pivotal role in ensuring adherence to legal requirements and standards. Properly educating staff members who handle weighing scales is essential to maintain accuracy, reliability, and legality in commercial applications.
Importance of Training Programs
Training programs on legal metrology provide in-depth knowledge on the legal requirements governing the use of weighing scales. These programs equip individuals with the necessary skills to operate weighing scales in compliance with international standards and regulations. By participating in such programs, employees gain a comprehensive understanding of legal metrology applications and are better equipped to handle measuring devices effectively.
Benefits of Ongoing Education
Continuous education in legal metrology ensures that staff members stay updated on the latest regulations and guidelines. Regular training sessions help reinforce good practices in the operation of weighing scales and promote a culture of compliance within the organization. By investing in ongoing education, businesses can prevent costly errors and maintain the integrity of their weighing processes.
Hands-On Workshops and Demonstrations
Practical training through hands-on workshops and demonstrations can significantly enhance the understanding of legal metrology requirements. These interactive sessions allow employees to familiarize themselves with the operation of different weighing scale types, verification procedures, and repair techniques. Hands-on experiences help reinforce theoretical knowledge and facilitate the application of legal metrology concepts in real-world scenarios.
8. Enhancing Compliance through Technology in Industrial Weighing Scales
In the ever-evolving landscape of legal metrology and compliance, incorporating advanced technology in industrial weighing scales has become crucial for businesses striving to meet regulatory standards. Leveraging technological advancements not only facilitates adherence to legal requirements but also enhances operational efficiency and accuracy in measuring instruments.
Automated Calibration Systems: Streamlining the calibration process is essential for ensuring accurate measurements and compliance with legal metrology regulations. Automated calibration systems, equipped with precision sensors and software algorithms, enable quick and reliable calibration of industrial weighing scales, reducing human error and minimizing the risk of non-compliance.
Integration of Data Management Software: Implementing data management software allows businesses to maintain comprehensive records of weighing scale operations, calibrations, and compliance activities. By centralizing data collection and analysis, organizations can track performance metrics, identify trends, and demonstrate adherence to legal metrology standards more effectively.
Remote Monitoring Solutions: Remote monitoring technology provides real-time insights into the performance and status of industrial weighing scales, allowing operators to proactively address issues and prevent downtime. Through remote access capabilities, businesses can remotely adjust settings, troubleshoot problems, and ensure continuous compliance with legal metrology requirements.
Incorporating Weighing Scale Automation: Embracing automation in weighing scale operations not only enhances efficiency but also reduces the likelihood of human errors that could lead to compliance issues. Automated processes for weighing, data recording, and reporting streamline operations while maintaining precision and consistency in measurements, aligning with legal metrology guidelines.
Harnessing IoT Connectivity: The Internet of Things (IoT) integration in weighing scales enables seamless communication between devices, systems, and stakeholders, fostering transparency and control over measurement processes. IoT-enabled scales can transmit data in real-time, monitor performance remotely, and generate automated reports for compliance audits, ensuring accuracy and reliability in commercial applications.
Enhancing compliance through technology in industrial weighing scales is not only about meeting legal standards but also about embracing innovation to drive operational excellence and competitive advantage in the market.
9. Maintaining Ongoing Compliance in Industrial Weighing Scales
Ensuring Compliance Through Regular Auditing:
To maintain ongoing compliance in industrial weighing scales, regular auditing plays a crucial role. Audits should be conducted periodically to assess if the scales meet the legal requirements set forth by relevant authorities. This process involves thorough inspections of each scale, verifying their calibration, and ensuring they adhere to the prescribed standards.
Conducting Internal Quality Control Checks:
Implement internal quality control checks as part of your compliance strategy. This involves internal audits and routine checks to monitor the accuracy and reliability of the weighing scales. By incorporating quality control measures within your operations, you can identify any deviations from legal metrology regulations proactively.
Training Staff on Legal Compliance:
Educate your staff on the legal compliance standards associated with industrial weighing scales. Training programs can help employees understand the importance of compliance, recognize common errors, and follow proper procedures when using the equipment. Well-informed staff contribute significantly to upholding regulatory requirements.
Documenting Maintenance and Calibration Practices:
Maintain detailed records of maintenance activities and calibration procedures for all weighing scales. Documentation should include dates of calibrations, repairs, and verification tests to demonstrate a diligent approach to compliance. Accurate record-keeping is essential for audit purposes and showcases your commitment to legal adherence.
Regular Communication with Suppliers and Service Providers:
Establish clear communication channels with suppliers and service providers involved in the maintenance and calibration of industrial weighing scales. Ensure that all parties are aware of the legal metrology requirements and work together to uphold compliance standards. Collaborative efforts facilitate a seamless compliance process and promote accountability.
Implementing Preventive Maintenance Schedules:
Develop preventive maintenance schedules to keep industrial weighing scales in optimal condition. Regular servicing, inspections, and recalibrations prevent potential issues and ensure continued compliance with legal metrology regulations. Proactive maintenance practices extend the lifespan of the equipment and minimize the risk of non-compliance.
Engaging with Regulatory Authorities:
Stay informed about updates and changes in legal metrology regulations by engaging with regulatory authorities. Seek guidance from the national institute of standards or the legal metrology department to stay abreast of evolving requirements. Proactive engagement demonstrates your commitment to compliance and fosters a cooperative relationship with regulatory bodies.
Utilizing Technology for Compliance Management:
Leverage technological solutions for compliance management in industrial weighing scales. Automated systems for data collection, reporting, and compliance tracking streamline operational processes and enhance accuracy. Integrating technology into compliance practices reinforces efficiency and transparency in adherence to legal standards.
Conclusion
In the complex realm of industrial weighing scales legal compliance, understanding the regulations and requirements is crucial for smooth operations and industry credibility. By demystifying these guidelines in our complete guide, we have empowered you with the knowledge to navigate the intricate landscape of regulatory compliance confidently. With a focus on precision and accuracy, our insights aim to elevate your woodworking business to new heights of success. Implementing compliant weighing solutions not only ensures adherence to legal standards but also enhances operational efficiency and customer trust. Ready to unlock the full potential of your woodworking business? Take the first step towards compliance and excellence by exploring our range of industrial weighing scales tailored to meet your specific needs. Elevate your operations with precision and confidence – because in the woodworking industry, compliance is key to sustainable
FAQ
What are some common legal pitfalls in industrial weighing scales compliance?
Some common legal pitfalls in industrial weighing scales compliance include: Non-compliance with local or national measurement standards and regulations Inaccurate or inconsistent readings due to faulty equipment or improper calibration Lack of proper documentation and record-keeping, leading to potential legal disputes Failure to adhere to safety regulations and protocols, resulting in workplace accidents or injuries.
What are the key components of legal compliance in industrial weighing scales?
Key components of legal compliance in industrial weighing scales include accuracy, calibration, and certification. Accuracy refers to the precision with which the scale measures weight and must meet the standards set by the government. Calibration ensures that the scale is functioning correctly and must be done regularly. Certification is required for the scale to be used in trade and must be obtained from a government-approved agency.
Why is legal compliance important in industrial weighing scales?
Legal compliance is important in industrial weighing scales because it ensures that the scales are accurate and meet the necessary standards set by regulatory bodies. This ensures fairness in trade and prevents fraud. Non-compliant scales can result in penalties and loss of trust in the business. It also ensures the safety of workers who use the scales, as well as the accuracy of data for record-keeping and decision-making.
What are the legal requirements for industrial weighing scales?
The legal requirements for industrial weighing scales vary depending on the country and industry. In general, industrial scales must meet accuracy standards set by the government and undergo regular calibration and maintenance. They may also need to be certified and approved by a regulatory body. Additionally, some industries may have specific regulations for the use of weighing scales, such as for food production or pharmaceutical manufacturing. It is important for businesses to research and comply with all relevant laws and regulations when using industrial weighing scales.
What documentation is needed for compliance in industrial weighing scales?
In order to comply with legal requirements for industrial weighing scales, you will need to have certain documentation in place. This may include: Certificate of Conformance: This certifies that the scale meets all necessary legal requirements and specifications. Calibration Certificate: This verifies that the scale has been calibrated to meet accuracy standards. Test Report: This provides detailed information on the scale’s performance during testing. User Manual: This outlines proper usage and maintenance instructions for the scale. Service and Maintenance Records: This documents any repairs or maintenance performed on the scale.
How can I ensure accuracy and precision in industrial weighing scales?
To ensure accuracy and precision in industrial weighing scales, it is important to follow these steps: Regular Calibration: Make sure to calibrate your weighing scales regularly according to the manufacturer’s instructions. This will ensure that the scale is measuring accurately. Proper Use: Use the weighing scale correctly and follow the manufacturer’s guidelines for loading and operation. Avoid placing objects on the scale that exceed its maximum capacity. Level Surface: The weighing scale should be placed on a flat and stable surface to avoid any discrepancies in measurement. Maintenance: Regularly clean and maintain the weighing scale to ensure its accuracy. Check for any wear and tear and replace any damaged parts. Legal Compliance: Make sure that your weighing scale meets all legal requirements and standards set by the government.