Master Your Measurement: Top 5 No Fail Tips for Industrial Scale Users
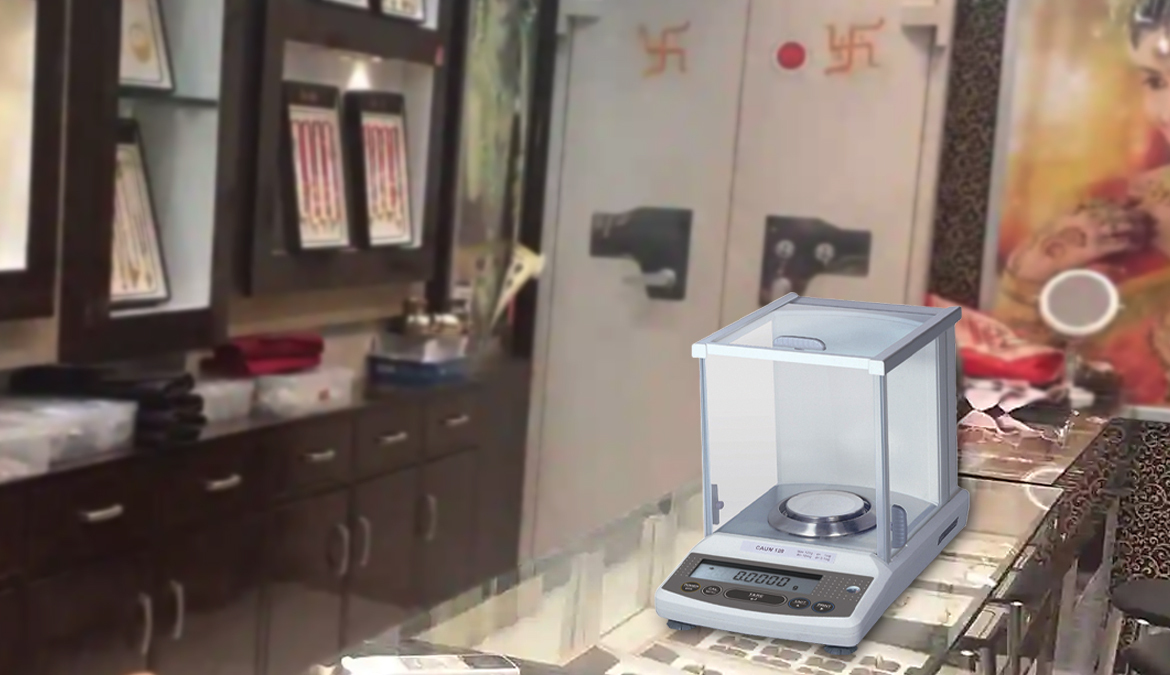
Are you puzzled about mastering industrial scale measurements? Imagine effortlessly acing your measurements every time, eliminating errors, and boosting efficiency. We’ve got you covered with our top 5 no-fail tips for industrial scale users. Let’s dive in and unlock the secrets to precision and accuracy in your measurement processes.
In this blog, we’ll address common pain points faced by industrial scale users, offering practical solutions and expert insights. Here’s a sneak peek of what we’ll cover:
Understanding the importance of calibration in maximizing accuracy and reliability.
Exploring the significance of proper maintenance for prolonging the lifespan of your industrial scale.
Unveiling tips for selecting the right scale for your specific needs and applications.
Discovering ways to troubleshoot common issues and ensure smooth operations.
Learning best practices for data interpretation and analysis to drive informed decision-making.
Get ready to revolutionize your measurement practices and elevate your efficiency to new heights.
Short Summary
- Calibration is crucial for maximizing accuracy and reliability in industrial scale measurements.
- Proper maintenance is essential for extending the lifespan of your industrial scale.
- Selecting the right scale tailored to your specific needs is key for accurate measurements.
- Troubleshooting common issues ensures smooth operations and efficiency in your measurement processes.
Table of Contents
Toggle1. Understanding Load Cells and Weighing Systems
What are Load Cells?
Load cells are transducers that convert mechanical force into electrical signals. They are an essential component of weighing systems, providing accurate weight measurements in various industrial applications.
Types of Load Cells:
- Strain Gauge Load Cells
- Hydraulic Load Cells
- Pneumatic Load Cells
Importance of Load Cell Accuracy:
Ensuring the accuracy of your load cell is crucial for obtaining reliable weight measurements. Factors such as environmental conditions, response time, and maximum deviation can impact the precision of a load cell.
Common Scale Errors:
- Environmental Factors: Changes in temperature and air pressure can affect load cell performance.
- Mechanical Force: Shock loading or excessive force can lead to inaccurate readings.
- Static Electricity: Build-up of static electricity can interfere with weight measurements.
Tips for Reliable Weighing Systems:
- Regularly calibrate your weighing system to maintain accuracy.
- Consider the maximum capacity and response time of your load cell.
- Install load cells on a stable, level surface to prevent errors.
- Avoid overloading the scale platform to ensure long-term performance.
- Control environmental factors such as temperature and humidity for consistent measurements.
2. Importance of Load Cell Accuracy in Weight Measurement
When it comes to weight measurement, one crucial factor that cannot be overlooked is the accuracy of the load cell. Load cells are the heart of any weighing system, as they are responsible for converting mechanical force into an electrical signal that can be translated into a weight reading. Here are some key points to consider regarding the significance of load cell accuracy in weight measurement:
- Precision for Reliable Readings
Ensuring the accuracy of load cells is essential for obtaining precise and dependable weight readings. A high level of accuracy is crucial, especially in industrial settings where even a small deviation can result in significant errors.
- Avoiding Common Mistakes
Common mistakes such as environmental factors, maximum deviation of a load cell, and response time can all impact the accuracy of weight measurements. By maintaining the accuracy of load cells, these errors can be minimized, leading to more reliable results.
- Impact on Scale Performance
The accuracy of load cells directly influences the overall performance of a weighing scale. Inaccurate load cells can lead to inconsistent and incorrect weight measurements, affecting the efficiency and reliability of the scale.
- Ensuring Safety and Compliance
In industries where precise weight measurements are critical for safety and regulatory compliance, the accuracy of load cells plays a crucial role. Maintaining accurate load cells ensures that weight measurements meet required standards and guidelines.
3. Common Mistakes Impacting Scale Accuracy
When it comes to industrial scale users, ensuring accuracy in measurements is crucial for maintaining operational efficiency and quality standards. However, there are common mistakes that can significantly impact scale accuracy if not addressed properly. Let’s delve into these pitfalls and explore solutions to optimize your weighing system:
Lack of Regular Calibration
Regular calibration is the cornerstone of maintaining accurate weight measurements. Failure to calibrate your scale at recommended intervals can lead to drift, causing inaccuracies in readings over time. To address this, establish a routine calibration schedule and adhere to it diligently to ensure consistent and precise results.
Environmental Factors
Environmental factors such as temperature variations, humidity levels, and air pressure can influence the performance of your weighing system. Sudden changes in these conditions may affect the accuracy of measurements, leading to errors. To mitigate this, consider installing your scale in a controlled environment and implement measures to minimize environmental fluctuations.
Overloading the Scale
Exceeding the maximum capacity of your scale or subjecting it to shock loading can cause mechanical strain and compromise accuracy. Avoid overloading your scale beyond its designated limit to prevent damage to the load cells and ensure reliable measurements. Additionally, educate operators on proper loading procedures to prevent inaccuracies caused by inconsistent weight distribution.
Neglecting Maintenance
Regular maintenance is essential for preserving the functionality and accuracy of your weighing system. Neglecting routine checks, cleaning, and repairs can lead to deteriorating performance and unreliable readings. Create a maintenance schedule that includes inspecting load cells, cleaning scale platforms, and addressing any issues promptly to maintain optimal accuracy.
Improper Installation
Incorrect installation, such as placing the scale on an uneven surface or failing to secure components properly, can introduce errors into weight measurements. Ensure that your scale is installed on a stable foundation, such as a pit foundation for truck scales, to minimize vibrations and ensure consistent readings. Follow manufacturer guidelines for installation to avoid inaccuracies due to improper setup.
Inadequate Training
Insufficient training for users operating the weighing system can result in errors and inaccuracies. Providing comprehensive training on scale operation, maintenance procedures, and troubleshooting techniques is essential for optimizing accuracy. Invest in employee training to enhance operational proficiency and minimize the risk of errors impacting measurements.
Addressing these common mistakes effectively can help industrial scale users enhance the accuracy and reliability of their weighing systems, ensuring precise weight measurements for operational success.
4. Factors Affecting Scale Accuracy and Measurement Precision
When it comes to ensuring precise and reliable scale measurements, understanding the factors that can impact accuracy is crucial for industrial scale users. Let’s delve into the key elements that influence scale accuracy and measurement precision:
- Environmental Factors:
Temperature Fluctuations: Changes in temperature can affect the performance of load cells, leading to measurement errors. It’s essential to maintain a consistent temperature in the weighing area to minimize this impact.
Humidity Levels: High humidity can interfere with electrical signals, causing disruptions in weight measurement readings. Keeping the weighing environment dry can help improve accuracy.
Vibration and Mechanical Force: Vibrations or external forces applied to the scale platform can introduce errors in weight measurements. Ensuring a stable and secure setup can mitigate these issues.
- Load Cell Considerations:
Response Time: The speed at which a load cell responds to weight changes is critical for accurate measurements. Opting for load cells with fast response times can enhance measurement precision.
Maximum Capacity: Exceeding the maximum capacity of a load cell can lead to inaccurate readings. It’s essential to select a load cell that aligns with the weight requirements of your application.
Calibration and Maintenance: Regular calibration and maintenance of load cells are necessary to preserve accuracy over time and prevent deviations in measurement precision.
- Error Types and Mitigation:
Common Scale Errors: Understanding the various types of errors, such as zero errors, non-linearity, and hysteresis, can help identify and address inaccuracies in weight measurements.
Static Electricity and Shock Loading: Static electricity buildup or sudden shock loading can impact scale accuracy. Implementing grounding measures and avoiding abrupt weight changes can minimize these issues.
- Scale Installation Considerations:
Pit Foundation: The construction of a stable and level pit foundation for the scale platform is essential for accurate measurements, as uneven surfaces can lead to errors.
Controlled Environment: Creating a controlled environment free from external influences like dust, air pressure variations, and electrical interference is crucial for maintaining measurement precision.
By addressing these factors and implementing best practices in environmental control, load cell selection, error mitigation, and scale installation, industrial scale users can optimize accuracy and measurement precision, ensuring reliable weight readings for their operations.
5. Enhancing Accuracy and Reliability in Weight Measurement
Ensuring accurate weight measurement is crucial for industrial scale users to maintain efficiency and avoid costly errors. Here are some key tips to enhance the accuracy and reliability of weight measurement in your operations:
- Calibration and Maintenance:
Regular calibration of your weighing system is essential to ensure accuracy. Keep a detailed maintenance schedule and adhere to it diligently.
- Environmental Considerations:
- Control environmental factors such as temperature, humidity, and air pressure to minimize interference with weight measurements.
- Temperature control in the weighing area.
- Avoiding exposure to direct sunlight or drafts.
- Implementing humidity controls in sensitive environments.
- Load Cell Considerations:
- Understand the maximum capacity and response time of your load cell to avoid overloading and ensure accurate readings.
- Maximizing Load Cell Accuracy
- Regularly check load cell performance.
- Monitor and record response times for analysis.
- Avoid shock loading to prolong load cell life.
- Error Reduction Strategies:
- Identify common mistakes that lead to inaccurate readings and implement strategies to mitigate errors effectively.
- Common Scale Errors to Avoid
- Educate operators on proper use of the weighing scale.
- Address mechanical force issues promptly.
- Implement anti-static measures in environments prone to static electricity.
- Quality Assurance Protocols:
- Develop quality control procedures to validate the accuracy of weight measurements and maintain consistency in results.
- Ensuring Accurate Weight Measurements
- Conduct regular checks on scale platform integrity.
- Implement a weight controller system for real-time monitoring.
- Verify accuracy of load sensors through periodic testing.
By implementing these tips and best practices in weight measurement, industrial scale users can enhance the accuracy and reliability of their operations, leading to improved efficiency and reduced risks of errors.
Conclusion
In conclusion, mastering measurement in industrial scale usage is crucial for woodworking success. By implementing the top 5 no-fail tips shared in this blog, you are well on your way to achieving precision and efficiency in your projects. Remember, accurate measurement is the foundation of quality craftsmanship and can make or break your final product. As a trusted authority in the woodworking industry, we are committed to equipping you with the knowledge and tools necessary for success. Stay tuned for more valuable insights and expert advice to elevate your woodworking skills. Ready to take your woodworking to the next level? Start implementing these tips today and experience the difference in your projects. Embrace precision, efficiency, and quality in every measurement – your woodworking legacy depends on it. Master your measurement and
FAQ
What factors can affect scale accuracy and measurement precision?
There are several factors that can affect scale accuracy and measurement precision, including temperature, humidity, vibrations, and external forces. It is important to regularly calibrate and maintain your scale to ensure accurate and precise measurements. Additionally, using a stable and level surface, avoiding overloading the scale, and handling the scale gently can also help improve accuracy and precision.
How can common mistakes impact scale accuracy?
Common mistakes such as improper placement, overloading, and incorrect calibration can significantly impact the accuracy of industrial scales. For example, placing the scale on an uneven surface or using it in an environment with extreme temperature or humidity can affect the readings. Overloading the scale beyond its capacity can also cause inaccurate measurements. Additionally, not calibrating the scale regularly can lead to errors in measurements.
How do load cells work on industrial scales?
Load cells are a vital component of industrial scales, responsible for converting the weight applied to the scale into an electrical signal. They work by utilizing strain gauges, which change resistance when force is applied, and this change in resistance is translated into an electrical signal that can be measured by the scale’s digital display. The more weight applied to the scale, the greater the resistance change and the higher the electrical signal. This allows for accurate and precise weight measurements in industrial settings.
What is the importance of load cell accuracy in weight measurement?
Load cell accuracy is crucial in weight measurement for industrial scale users because it directly impacts the accuracy of the final weight readings. Even small errors in load cell accuracy can result in significant discrepancies in weight measurements, which can lead to costly errors or safety hazards. Therefore, it is essential to regularly calibrate and maintain the accuracy of load cells to ensure precise and reliable weight measurements.
What steps can be taken to enhance accuracy and reliability in weight measurement for industrial scales?
Here are five tips to ensure accuracy and reliability in weight measurement for industrial scales: Regularly calibrate your scales: Regular calibration is crucial for maintaining accurate and reliable measurements. Make sure to follow the manufacturer’s recommendations for calibration frequency. Keep the scales clean: Dust, debris, and other contaminants can affect the accuracy of your measurements. Regularly clean your scales to ensure reliable results. Use the correct units: Make sure to use the correct units of measurement for your specific application. This can help avoid errors and ensure consistency in your measurements. Train your operators: Proper training is essential for accurate weight measurement. Make sure your operators are familiar with the scale’s functions and know how to use it properly.